Formwork Types
Formwork can be made from a variety of products, consisting of hardwood, steel, and prefabricated panels, and have to be made to hold up against the pressure of the concrete as it is poured and cured. Selecting appropriate types of formwork in construction is crucial to the success of any building project. Each sort of formwork has unique benefits and challenges, and choosing the best one depends upon the task's size, complexity, spending plan, and ecological goals. additional hints formwork systems integrate modular elements, normally made from metal (steel or aluminium) or plastic.
It incorporates the erection of any kind of type of building framework, whether a building, a bridge, or perhaps a skyscraper. To make sure safety and security and security, the formwork system should be effectively supported and secured. The formwork should be made to stand up to the wind and various other environmental elements that might trigger it to collapse. The formwork system have to also be developed to enable simple accessibility and egress for employees.
Understanding the various types of formwork, their details applications, and the technical criteria governing them is necessary for accomplishing top quality and safety and security. Plastic formworks are gently weighted, interlacing systems and can be utilized more than 100 times. This sort of formwork is currently coming to be popular for similar shapes and large real estate plans. Formwork is the structure for any kind of concrete building and construction job, with each structural formwork aspect being made according to the structure they are sustaining. Even resilient formwork systems like steel and light weight aluminum require normal inspection to guarantee they stay in excellent condition.
Sorts of Formwork
Formwork is a crucial part in the construction industry, providing the short-term framework that shapes and sustains fresh concrete till it solidifies. Different sorts of formwork are employed, each serving certain construction demands and offering distinctive benefits. From conventional hardwood forms to contemporary modular systems, comprehending the various kinds of formwork helps in choosing the appropriate solution for effectiveness, cost-effectiveness, and top quality in structure projects.
With a concentrate on innovation and performance, industry specialists have to stay attentive in adopting and adapting to these changes. In addition, the integration of automation in formwork installment is reshaping just how building and construction tasks are undertaken. Technologies such as robotic systems and automated lifting gadgets are simplifying the processes associated with setting up and dismantling formwork.
1. Standard Formwork
Traditional formwork is among the most widely used sorts of formwork in building. This technique entails the use of wooden boards, steel plates, or plywood to create molds for concrete pouring. The products are usually put together on-site to guarantee an exact fit for the particular framework being constructed. As a functional and cost-efficient option, typical formwork is favored for a selection of tasks, consisting of residential buildings, bridges, and retaining walls.
One of the vital benefits of standard formwork is its adaptability. It can be quickly formed and adapted to satisfy the special demands of different designs. In addition, the materials used are commonly readily offered, making them an obtainable alternative for professionals. Nonetheless, the arrangement process can be labor-intensive and lengthy, which can impact total project timelines.
One more factor to consider with traditional formwork is its sturdiness. While it can execute well for temporary applications, repeated usage may cause deterioration, requiring substitute after a limited variety of cycles. This can enhance lasting costs compared to more modern alternatives, such as modular or recyclable formwork systems. Nevertheless, typical formwork remains a popular selection due to its simplicity and efficiency in attaining strong architectural outcomes.
2. Modular Formwork
Formwork is a crucial element in the building industry, offering a short-term structure to support freshly put concrete until it obtains sufficient stamina. Amongst the various types of formwork readily available, modular formwork stands out as a result of its adaptability and effectiveness.
Modular formwork consists of prefabricated panels and elements that can be quickly put together and disassembled. This system permits quick building and can be customized to fit different job requirements. The panels are typically made from products such as steel, light weight aluminum, or premium wood, guaranteeing resilience and strength. With modular formwork, building groups can enhance labor and lower waste, as the panels can be reused for multiple projects.
One more advantage of modular formwork is its adaptability in layout. The panels can be reorganized to produce numerous sizes and shapes, accommodating both basic and complicated frameworks. This adaptability makes it appropriate for a variety of applications, from residential buildings to huge infrastructure projects.
In general, modular formwork offers an efficient, cost-efficient, and adaptable solution for supplying high-grade concrete frameworks while decreasing time and effort on construction websites.
3. Slipform Formwork
Slipform formwork is a continual technique of developing concrete structures that permits the formwork to relocate vertically as the concrete is poured. This technique is especially useful for high structures, such as skyscrapers, silos, and bridges, as it enables a smooth building procedure with marginal disruption.
One of the major benefits of slipform formwork is its capacity to produce smooth surfaces and uniform frameworks due to the continuous pouring technique. This decreases the demand for finishing job after the concrete has established, saving both time and labor costs. In addition, slipform systems can be customized to fit numerous sizes and shapes, making them flexible for different construction projects.
The procedure of slipform formwork entails a mechanized system that elevates the formwork as the concrete hardens, providing a regular rate of ascent. This method not only enhances the speed of building and construction yet additionally enhances the structural stability of the final product by minimizing cool joints, which can take place when concrete is gathered different batches.
Regardless of its benefits, slipform formwork calls for mindful preparation and skilled labor to guarantee the devices works properly and the concrete is of adequate high quality. Ample guidance and surveillance are necessary to take care of the concrete's setting procedure and preserve the upright placement of the formwork.
4. Taskform Formwork
Formwork is a vital element in building and construction, providing a temporary framework to sustain freshly poured concrete up until it solidifies. There are different sorts of formwork, each with unique qualities and applications. One noteworthy type is Taskform formwork, made for effectiveness and ease of usage in a range of building projects.
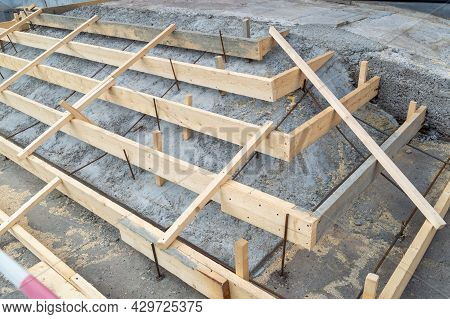
Taskform formwork is commonly made from lightweight products, making it much easier to take care of and move. This type of formwork is known for its modular design, permitting fast setting up and disassembly. Its adaptability allows it to be used in various applications, from foundations to wall surfaces and columns. The versatility of Taskform formwork not only minimizes labor prices yet likewise minimizes building and construction time, making it a popular selection amongst service providers.
In addition, Taskform formwork supplies superb surface finishes, leading to top notch concrete frameworks. Its accuracy engineering ensures uniformity in dimensions, which is vital for structural stability. With the option for various setups, Taskform formwork can suit complicated styles and differing task needs, additionally boosting its charm in modern-day construction practices.
5. Stay-in-place Formwork
Stay-in-place formwork is a building and construction approach that includes using long-term materials that continue to be in the ended up structure. This sort of formwork offers both architectural assistance during the healing of concrete and serves as a permanent element of the structure. Stay-in-place formwork systems are popular for their effectiveness and capability to lower labor costs and time on-site.
One of the typical materials utilized for stay-in-place formwork is insulated concrete types (ICFs), which use excellent thermal insulation properties. These types are generally made from broadened polystyrene or comparable products, enabling very easy handling and setup. Once the concrete is put and healed, the kinds stay in area, offering extra insulation and strength to the wall surfaces.
An additional kind of stay-in-place formwork is pre-cast concrete panels. These panels are manufactured off-site and transferred to the building location, where they are erected and attached. This approach not just accelerates construction yet also makes sure premium coatings, as the panels can be dealt with or covered prior to installment.
Stay-in-place formwork also consists of systems made from metal, such as steel or light weight aluminum. These materials can be reused but are likewise left in place, adding to the building's architectural integrity. Steel stay-in-place formwork is particularly useful in high-rise building and constructions where additional assistance and resilience are needed.
Overall, stay-in-place formwork provides a variety of advantages, consisting of reduced building and construction time, enhanced thermal efficiency, and increased structural toughness. Its flexibility makes it a significantly popular selection in modern building projects, specifically in energy-efficient style.
6. Precast Formwork
Precast formwork describes a type of formwork that is produced off-site and afterwards transported to the construction location. This strategy involves producing concrete components in a regulated setting, which makes certain top quality and toughness. Once the precast elements are produced, they can be quickly assembled on-site, dramatically minimizing building and construction time.
One of the key benefits of precast formwork is its adaptability. It can be formed right into different sizes and shapes, permitting cutting-edge building layouts. In addition, the use of precast forms assists minimize labor costs, as less workers are needed for installation contrasted to traditional on-site formwork methods.
In addition, precast formwork can boost safety and security on building and construction sites. Given that several procedures occur in a manufacturing facility setting, the threats related to operating at elevations or managing wet concrete are lowered. This modular strategy likewise allows for better quality control, as each system is produced under optimal problems before being provided to the site.
However, one obstacle of precast formwork lies in transportation logistics. Correct preparation is necessary to guarantee that the parts come to the site in good problem and at the correct time. Furthermore, appropriate storage space for the precast modules is needed to stay clear of hold-ups and make sure efficient setting up on-site.
In recap, precast formwork offers a practical and effective option for modern construction projects, combining rate, safety, and style flexibility.
7. Protecting Formwork
Shielding formwork is a specialized kind of construction formwork designed to offer both structural assistance throughout the healing phase of concrete and thermal insulation for power efficiency. This formwork is particularly helpful in climates that experience extreme temperatures, minimizing the energy prices connected with heating or cooling down a structure.
Usually made from materials such as broadened polystyrene (EPS), phenolic, or polyurethane, insulating formwork not just forms the concrete yet also assists control temperature. This help in protecting against thermal cracking while guaranteeing the concrete maintains the proper conditions for healing. The insulation homes can dramatically influence the energy efficiency of buildings, leading to long-lasting cost savings in heating and cooling.
Shielding formwork can be made use of in numerous applications, including wall surfaces, roof coverings, and floorings, giving adaptability in building and construction. Additionally, once the concrete is set, the shielding panels can stay in place, contributing to the structure's overall insulation worth without the demand for additional products. This effectiveness makes insulating formwork a preferred choice in lasting building and constructions or projects going for higher energy efficiency criteria.
Traditional Formwork
Standard formwork is a critical component in the building and construction industry, acting as a short-term structure that sustains newly poured concrete until it solidifies and obtains toughness. Usually made from products such as wood or plywood, standard formwork has been widely made use of as a result of its cost and simplicity of setting up. With a variety of kinds customized to different building needs, standard formwork remains a preferred choice among home builders for forming wall surfaces, pieces, and other concrete aspects in both household and commercial jobs.
1.1 Products Used
Traditional formwork is a building and construction method commonly made use of for developing momentary structures that support concrete until it establishes and obtains enough stamina. The materials utilized in conventional formwork play a critical function in ensuring toughness and stability throughout the building and construction procedure. Different products are employed based upon availability, cost, and the details needs of the job.
- Wood: Frequently made use of as a result of its availability and ease of handling, lumber formwork can be reduced and formed to fit details layouts.
- Plywood: Commonly used for its toughness and smooth surface, plywood is regularly used in producing panel formwork.
- Steel: Known for its stamina and toughness, steel formwork can be recycled multiple times and is perfect for big or intricate structures.
- Aluminum: Lightweight and very easy to set up, aluminum formwork is getting popularity for its effectiveness and reusability.
- Plastic: Utilized for details applications, plastic formwork is light-weight and resistant to rust, making it an excellent alternative for certain types of projects.
Picking the best products is necessary to ensure the efficiency and effectiveness of typical formwork in various building circumstances.
1.2 Advantages
Typical formwork describes the use of wooden or steel frameworks to shape and sustain concrete till it sets. This technique has been a staple in construction due to its performance and integrity.
One of the primary benefits of traditional formwork is its versatility. It can be quickly personalized to fit a variety of sizes and shapes, making it ideal for numerous building jobs, from domestic structures to complicated frameworks.
One more key advantage is the cost-effectiveness of products. Numerous builders favor utilizing wood for conventional formwork because it is frequently more readily offered and cheaper than specialized formwork systems. This can result in significant savings in total project prices.
Furthermore, traditional formwork is reasonably very easy to assemble and disassemble, promoting quicker building and construction times. Proficient labor is commonly aware of this approach, reducing the learning contour and possible delays connected with more modern-day systems.
Additionally, typical formwork permits a high level of control over the concrete positioning, leading to better-quality coatings and architectural stability. This is specifically helpful when a smooth surface is required for aesthetic purposes or additional treatments.
Lastly, traditional formwork systems can be recycled several times, contributing to sustainability initiatives in building and construction. When handled properly, this reuse can lower waste and reduced the ecological impact of building jobs.
1.3 Downsides
Traditional formwork, typically made from wood or steel, is widely used in the building market for creating mold and mildews in which concrete is poured. However, regardless of its benefits, this technique has numerous negative aspects that can affect task performance and overall expenses.
One significant disadvantage of traditional formwork is the lengthy procedure involved in its configuration and taking down. Crafting the formwork to the accurate measurements required can postpone construction timelines and enhance labor expenses. This can lead to project overruns, especially in large applications where rate is necessary.
Additionally, traditional formwork is normally hefty and cumbersome, making it hard to deal with and transfer on-site. This weight not just contributes to labor expenses but can additionally cause safety and security hazards otherwise handled correctly. Additionally, employees may encounter physical pressure due to the manual work associated with assembling and dismantling the types.
Sturdiness is an additional worry. Wooden formwork, particularly, can warp or weaken with time, especially when revealed to dampness. While metal formwork is a lot more long lasting, it can still struggle with corrosion otherwise properly kept. This deterioration can cause jeopardized architectural stability and demand more frequent replacements or repair work.
In addition, traditional formwork frequently needs a significant quantity of material, causing greater product expenses. The demand for timber, metal, or other resources additionally raises environmental worries, specifically if sustainable practices are not prioritized in sourcing these materials.
Finally, traditional formwork has limited flexibility and versatility. As soon as created, the forms are usually designed for a particular pour, making it testing to customize them for various styles or measurements without considerable added job.
1.4 Applications
Conventional formwork, often described as conventional or lumber formwork, is widely utilized in the building and construction market for developing structural elements such as wall surfaces, pieces, and columns. Its style generally involves wood panels or boards that are protected with each other to create a mold and mildew for pouring concrete. This approach has been utilized for years due to its convenience and schedule of products.
One of the primary applications of traditional formwork is in household and commercial structure tasks. It is excellent for developing the structures, floorings, and upright elements of a structure, enabling the development of complex forms and surface areas. In addition, standard formwork is frequently used in framework projects, such as bridges and tunnels, where tailored shapes are essential to sustain the structural stability.
An additional considerable application is in remodelling and repair work. When existing structures need enhancements or modifications, typical formwork can be adapted to fit the details needs of the job. This adaptability makes it a recommended choice for service providers that require to exactly shape their concrete pours to meet architectural standards.
Moreover, standard formwork is frequently employed in the precast concrete industry. It enables the manufacturing of different precast elements like light beams, pieces, and panels, which can after that be transported and put together on-site. This aids quicken construction timelines and ensures high-grade coatings.
In recap, typical formwork plays an important role in a large selection of building and construction applications, providing adaptability and performance for various architectural needs.
Modular Formwork
Modular formwork is a versatile building and construction approach that streamlines the procedure of producing concrete frameworks. Making up premade components that can be reused and reconfigured, this system advertises efficiency and cost-effectiveness on building sites. By enabling fast setting up and disassembly, modular formwork not just lowers labor time however additionally reduces material waste, making it an environmentally friendly option. With various layouts offered, it accommodates different task needs, from domestic structures to big infrastructure works.
2.1 Materials Made use of
Modular formwork is a functional building and construction system that uses standardized parts to develop temporary frameworks for concrete puts. The materials made use of in modular formwork are essential in figuring out the efficiency, sturdiness, and cost-effectiveness of the system. Various products are utilized to make sure that the formwork can hold up against the stress and anxieties of concrete pouring and preserve its form up until the concrete collections.
- Steel: Recognized for its stamina and resilience, steel is frequently made use of in modular formwork systems, providing architectural security and the capacity to be reused multiple times.
- Light weight aluminum: Lightweight yet solid, light weight aluminum formwork is less complicated to manage and set up, lowering labor costs while still offering sufficient load-bearing abilities.
- Plywood: Generally used as an encountering material, plywood can be utilized in combination with various other products to produce a cost-effective and versatile formwork solution.
- Plastic: Some modular systems utilize high-density polyethylene or various other plastics, which are immune to weather and chemical exposure, making them appropriate for various settings.
- Composites: Innovative composite products can be developed to provide enhanced properties, such as boosted insulation, decreased weight, and increased longevity.
Each of these products serves certain purposes depending on the job needs, making modular formwork a flexible solution for numerous construction applications.
2.2 Advantages
Modular formwork systems give a functional and effective option for various construction tasks. These formwork systems are developed to be adaptable and multiple-use, considerably improving the building process while decreasing product waste and labor expenses.
Among the main benefits of modular formwork is its speed of setting up and disassembly. Because the elements are standardized, they can be promptly assembled on-site, allowing for faster concrete pouring and minimizing task timelines. This effectiveness can cause overall expense savings and boosted task deliverables.
One more benefit is the adaptability supplied by modular formwork. It can be conveniently configured to fit numerous layout sizes and shapes, making it ideal for various types of structures. This adaptability enables the building of complicated building functions without the need for custom formwork remedies.
Modular formwork is likewise understood for its durability and strength. Made from high-grade materials, it can endure the stress of damp concrete while keeping its shape and architectural honesty. This integrity makes certain that the final product satisfies top quality and safety standards.
Additionally, making use of modular formwork promotes sustainability in construction. Because the system is recyclable, it lessens the demand for new products for each job, contributing to much less waste and lower environmental effect. This element is significantly crucial in today's eco-conscious structure practices.
Finally, the advantages of modular formwork-- such as rate, adaptability, resilience, and sustainability-- make it an outstanding selection for modern-day building jobs, allowing home builders to fulfill expanding demands while keeping high quality and performance.
2.3 Downsides
Modular formwork systems provide various benefits in building and construction, yet they likewise have some significant downsides that can impact their viability for specific jobs.
One major disadvantage is the preliminary price of purchasing or renting modular formwork. While they might result in cost financial savings in labor and time, the ahead of time financial investment can be considerable, making it less appealing for smaller sized tasks with restricted budget plans.
One more concern is the requirement for experienced labor to construct and disassemble the formwork appropriately. Improper installment can bring about architectural issues, which could endanger the safety and security and integrity of the building. This reliance on knowledgeable employees can even more raise job costs and timelines.
Furthermore, modular formwork systems may not always be adaptable to complicated or uneven forms. While they excel in standard tasks, personalized layouts can present obstacles, leading to potential hold-ups and boosted labor efforts.
Transport and storage space can also position challenges, as modular components are typically bulky and require appropriate room. This can make complex logistics, particularly on sites with restricted gain access to or room restrictions.
Ultimately, there might be limitations on the kinds of concrete mix that can be made use of with particular modular systems. Some forms might react improperly with particular chemical structures, which can influence the total quality of the concrete and the toughness of the framework.
2.4 Applications
Modular formwork systems have actually come to be a criterion in the building sector because of their convenience and effectiveness. These systems are designed to be multiple-use and versatile, making them suitable for numerous applications.
One primary application of modular formwork is in the construction of wall surfaces and slabs. The capacity to easily put together and disassemble components enables fast configurations, which dramatically decreases labor time and expenses. This is particularly useful in massive projects where speed is important.
One more substantial application is in the development of complex structures. Modular formwork can be customized to fit special building styles, enabling contractors to accomplish detailed shapes and kinds without jeopardizing structural integrity. This adaptability makes it a recommended option for both domestic and business buildings.
In addition, modular formwork is widely used in infrastructure tasks such as bridges, passages, and maintaining wall surfaces. The robust building of these systems ensures they can hold up against the pressures of heavy concrete pours and supply exact dimensional control, crucial for secure and effective project conclusion.
Moreover, modular formwork is increasingly being used in sustainable building methods. Its recyclable nature decreases waste and lowers the environmental effect of construction tasks. By advertising efficiency, these systems line up with the growing concentrate on green structure methods.
Generally, the adaptability and performance of modular formwork make it a crucial tool across various building and construction applications, adding to the modern-day improvement of building methods.
Slipform Formwork
Slipform formwork is a cutting-edge construction technique extensively used for creating upright structures, such as silos, towers, and high-rise buildings. This technique entails a continuously relocating form that allows concrete to be put without stops briefly, leading to smooth, smooth finishes. As a very effective option to conventional formwork systems, slipform innovation provides enhanced rate and structural integrity, making it a vital option for modern-day building projects. Its versatility to numerous designs further boosts its popularity in the industry.
3.1 How It Functions
Slipform formwork is a contemporary building and construction method utilized for creating upright structures such as walls, silos, and towers. This approach entails the constant pouring of concrete right into a moving formwork, allowing for smooth and uninterrupted building and construction. Unlike standard formwork, which is set up and afterwards removed after the concrete has actually established, slipform formwork is developed to move up as the concrete treatments, commonly at a price that matches the setting time of the concrete being put.
The procedure starts with a stationary base that acts as the foundation for the formwork. As soon as the base is safe and secure, the slipform is set in location and straightened. As concrete is constantly put into the kind, hydraulic jacks or mechanical systems gradually raise the slipform. This higher movement signifies the next area of the wall surface or structure being built. As the slipform ascends, the concrete below starts to establish, making sure that the framework keeps its stability and toughness.
Among the essential advantages of slipform formwork is its effectiveness in creating high structures. As the form moves, it reduces the need for labor-intensive procedures commonly related to conventional formwork systems. The continual process not only speeds up building time however additionally lowers the capacity for joints or joints within the concrete, which can cause structural weaknesses.
Additionally, slipform modern technology permits accurate control of the concrete's positioning and uniformity, resulting in high-quality surfaces. It is especially advantageous in projects needing considerable height and quantity, such as high-rise buildings, parking garages, and commercial silos, making it a popular selection for contemporary construction methods.
3.2 Benefits
Slipform formwork is a cutting-edge building approach that uses a number of advantages over conventional formwork systems. This method uses a continuous putting process, enabling structures to be constructed at a faster rate and with better efficiency.
Among the primary benefits of slipform formwork is its ability to help with continuous building. By permitting undisturbed pouring of concrete, jobs can be finished in much less time compared to traditional techniques, which usually call for the disassembly and reassembly of forms after each area is poured.
An additional advantage is the improved structural integrity attained via the uniformity of the poured concrete. The seamless building and construction reduces joints and weak points in the structure, resulting in a much more secure and long lasting end product. This is especially essential for skyscrapers and various other frameworks based on significant stress and anxiety.
In addition, slipform formwork reduces labor prices and boosts safety and security on site. Considering that the system is mechanized and continual, the need for substantial labor to handle or adjust conventional kinds is significantly reduced. This leads to less security dangers related to manual handling of hefty products.
Lastly, this technique supplies design adaptability, permitting the production of complex geometries and forms that might be testing to attain with various other formwork types. Architects and engineers can check out cutting-edge designs without jeopardizing on the usefulness or cost-effectiveness of the project.
3.3 Disadvantages
Slipform formwork, while providing numerous advantages in construction, additionally has a number of significant downsides that have to be thought about. Recognizing these disadvantages is necessary for job preparation and implementation.
Among the main downsides of slipform formwork is its high initial cost. The financial investment required for establishing and keeping the slipform system can be considerable, which might not be justifiable for smaller projects. This initial financial expense can deter some specialists from utilizing this approach.
Another significant disadvantage is the intricacy of the arrangement and operation. Slipform calls for knowledgeable labor and specialized devices, making it much less easily accessible compared to standard formwork systems. If the team does not have the necessary knowledge, it can result in delays and potential security dangers on-site.
In addition, slipform construction is highly depending on weather. Damaging climate can interfere with the continuous pouring procedure, bring about incongruities in the structure and possibly requiring therapeutic job. This reliance can influence task timelines and total effectiveness.
Finally, slipform formwork may be much less suitable for jobs that call for intricate designs or differing geometries. formwork regulations is primarily used for straightforward, vertical building and constructions, restricting its flexibility for complicated architectural features.
3.4 Applications
Slipform formwork is a flexible building and construction method primarily made use of for continual upright structures. This innovative strategy enables the development of high and complicated shapes, making it suitable for different applications in the building industry.
Among the most usual applications of slipform formwork is in the building and construction of skyscrapers. The ability to continually put concrete without the need for quiting at specific degrees contributes to raised performance and a faster conclusion time. This technique is specifically advantageous in the construction of cores for elevators and stairwells that call for a strong structural stability.
Another substantial application remains in the construction of silos and tanks. Slipform permits a smooth and uniform framework, which is crucial in storage applications for materials like grain, concrete, and liquids. The smooth indoor surfaces attained through slipform additionally help with much easier procedures and maintenance.
In addition, slipform formwork is often utilized for bridges and walkways. The constant nature of the construction provides itself well to creating the long, undisturbed spans necessary for modern-day highway systems, boosting both resilience and visual charm.
Lastly, slipform strategies are utilized in the advancement of , preserving wall surfaces, and numerous civil engineering jobs. The adaptability of this technique to produce varying heights and forms permits thorough options in metropolitan and rural setups alike, demonstrating its broad applicability in the building and construction market.
Taskform Formwork
Taskform Formwork concentrates on supplying a diverse variety of formwork systems that cater to different construction demands. By focusing on cutting-edge layout and efficient installment, Taskform uses remedies that enhance performance and make sure the greatest requirements of top quality in concrete construction. Recognizing the various sorts of formwork is crucial for home builders and service providers, as it plays a vital duty in attaining structural honesty and optimizing job timelines.
4.1 Meaning
Taskform Formwork refers to a details kind of formwork system designed for concrete construction jobs. This formwork is vital for forming and sustaining poured concrete till it gains enough toughness to hold itself up. The layout of Taskform systems permits fast setting up and disassembly, boosting performance on building websites.
Taskform Formwork typically consists of a variety of elements such as panels, frameworks, clamps, and devices, which can be set up in diverse ways to fit different structural shapes and sizes. It is especially preferred for its convenience, as it can be used in different applications including walls, slabs, and columns.
The system advertises labor efficiency and safety and security by decreasing hand-operated training and unpleasant positioning. Furthermore, Taskform Formwork is engineered to make certain a premium finish on the concrete surface, minimizing the need for extensive post-construction job.
In summary, Taskform Formwork represents a modern technique to concrete forming that promotes rate, flexibility, and quality in construction techniques.
4.2 Benefits
Taskform Formwork offers a number of advantages that improve building and construction performance and quality. These benefits make it a recommended choice in numerous tasks, from household builds to large business frameworks.
- Performance: Taskform's modular style enables quick setting up and disassembly, reducing labor time and general project period.
- Economical: The sturdiness and reusability of products result in considerable expense financial savings with time, as the formwork can be used for multiple tasks.
- Personalization: The system can be conveniently customized to fit various shapes and sizes, offering versatility for distinct architectural designs.
- High quality End Up: Taskform makes certain a smooth surface coating, lessening the requirement for added finishing work after concrete placement.
- Safety: The style integrates features that improve stability and security for workers, decreasing the dangers related to formwork installment.
4.3 Disadvantages
Taskform formwork is commonly utilized in building for different applications, yet it does include some drawbacks that ought to be taken into consideration when selecting the proper formwork type. Understanding these downsides can aid in making informed choices throughout the preparation and execution stages of construction tasks.
- High Initial Costs: The setup and products for Taskform formwork can be pricey, potentially enhancing the overall budget of a job.
- Labor-Intensive: The setup and removal procedure can call for substantial labor, causing boosted project timelines and expenses.
- Minimal Flexibility: Taskform may not be suitable for intricate layouts, which can restrict its application in much more complex constructions.
- Weight of Parts: The elements can be hefty, making transportation and managing more tough and needing more robust devices.
- Possible for Damages: The materials utilized in Taskform can be at risk to harm throughout setup and removal, causing extra substitute costs.
4.4 Applications
Taskform Formwork provides versatile services for numerous building applications, enabling efficient and reliable concrete positioning. Its modular design enables quick assembly and disassembly, making it ideal for both massive jobs and smaller sized constructions.
One considerable application of Taskform Formwork is in the construction of skyscrapers. The lightweight elements assist in fast upright construction, while the robust attributes guarantee structural stability throughout the setup of concrete. Furthermore, the ability to adapt the formwork to different building styles improves its energy in metropolitan growth.
One more notable use Taskform Formwork remains in the building and construction of retaining walls and structures. The system can hold up against substantial pressure from wet concrete, offering a trusted solution for deep excavations and heavy loads. This capability is crucial for projects that call for durable and long-lasting frameworks.
In Addition, Taskform Formwork is excellent for civil engineering tasks such as bridges and tunnels. Its versatility allows builders to tailor the formwork to the needed forms and measurements, ensuring a seamless fit and finish. This flexibility not only streamlines the construction process however likewise enhances the last high quality of the concrete surface.
In industrial applications, Taskform Formwork verifies beneficial for developing customized frameworks, including silos and storage tanks. The system's aesthetic versatility and toughness aid satisfy the needs for both useful and aesthetic allure in these tasks. Generally, the varied applications of Taskform Formwork highlight its relevance in modern-day construction practices.
Stay-in-place Formwork
Stay-in-place formwork is an innovative building method that entails using long-term formwork systems which remain in place after the concrete has healed. This type of formwork is made to give architectural assistance, insulation, and finishing in one incorporated remedy, therefore streamlining the structure process. By eliminating the demand for traditional removable types, stay-in-place systems boost efficiency and decrease labor expenses, making them a popular option in contemporary building and construction jobs.
5.1 Meaning
Stay-in-place formwork describes a sort of concrete formwork system that remains permanently in place after the concrete has actually been put and treated. This method supplies architectural assistance to the concrete element while additionally working as an insulating or securing layer. Stay-in-place formwork is generally made use of in various building applications, particularly in walls, pieces, and various other structural parts.
- Cost-Effective: Reduces labor prices given that the formwork does not require to be removed.
- Enhanced Thermal Efficiency: Frequently consists of insulating residential or commercial properties that boost power effectiveness.
- Architectural Stability: Gives additional strength and resilience to the concrete when treated.
- Minimized Waste: Minimizes the demand for traditional formwork materials, advertising sustainability.
- Design Flexibility: Can be customized to fit numerous architectural styles and demands.
5.2 Benefits
Stay-in-place formwork, additionally called permanent formwork, supplies several benefits in construction jobs. Unlike standard formwork, which is eliminated after the concrete has established, stay-in-place systems continue to be as an integral part of the structure, supplying ongoing benefits throughout its life-span.
One primary advantage is the decrease in labor expenses. Given that the formwork does not need to be dismantled and removed after the concrete has actually treated, the quantity of labor needed on-site is dramatically decreased. This can lead to faster job completion and lower general expenditures.
Another advantage is that stay-in-place formwork contributes to boosted structural stability. The constant existence of formwork can boost the sturdiness of the concrete, permitting it to better endure environmental tensions with time. This results in a more resilient and longer-lasting framework.
Additionally, stay-in-place formwork can improve insulation homes. Numerous systems are developed with protecting products that can aid keep comfortable temperature levels within the structure, lowering power consumption for heating & cooling.
Using stay-in-place formwork can likewise boost safety and security on-site. With fewer products to manage and get rid of, the threat of accidents connected to the handling of conventional formwork systems is minimized, creating a more secure working atmosphere for construction employees.
Lastly, the aesthetic allure of stay-in-place formwork ought to not be ignored. Many systems can integrate architectural finishes that get rid of the requirement for additional therapy, permitting layout flexibility and reduced finishing prices. This can result in an extra structured construction procedure and a visually pleasing final product.
5.3 Limitations
Stay-in-place formwork, additionally referred to as irreversible formwork, has actually come to be a popular option in building due to its capacity to stay indispensable to the ended up structure. However, this system likewise features constraints that should be taken into consideration when making layout and building and construction choices.
One limitation of stay-in-place formwork is the possibility for raised prices. While it can reduce labor and time during building, the initial products made use of, frequently concrete or premade components, can be a lot more expensive than typical detachable formwork. Additionally, if top notch materials are not utilized, there can be long-term upkeep expenses associated with degradation or damage in time.
An additional constraint is related to make flexibility. Stay-in-place formwork systems may not accommodate complicated designs as conveniently as traditional systems. This can limit designers and designers in their capability to execute unique and creative structural options, potentially bring about an extra standard layout technique.
In addition, the irreversible nature of stay-in-place formwork can additionally add to troubles in future renovations or adjustments. Once the formwork is in place, any type of requirement for change might be complicated and costly, as it may entail getting rid of areas of the structure that were indicated to be permanent.
Lastly, the performance of this formwork type can be affected by ecological variables. Exposure to dampness, temperature adjustments, and other external problems can influence the toughness and performance of the materials utilized. Correct assessments and protective procedures are required to mitigate these dangers, which can further complicate the building procedure.
5.4 Use Situations
Stay-in-place formwork is a building and construction method that produces structural elements while eliminating the need for conventional formwork removal. This system is specifically advantageous in different situations because of its performance, cost-effectiveness, and capability to improve the general longevity of frameworks. Below are some common use situations for stay-in-place formwork:
- Upright Elements: Ideal for developing wall surfaces, columns, and similar upright frameworks, offering assistance during the treating procedure.
- Slabs: Made use of in flooring and roofing pieces, providing constant support while acting as a permanent part of the structure.
- Bridges: Reliable for bridge construction, where formwork needs to stand up to not only the weight of the concrete however also varying environmental aspects.
- Basements: Generally used in the construction of below-grade walls, permitting a regular insulation layer.
- Specialized Applications: Suitable for one-of-a-kind architectural styles that need unconventional shapes or materials, simplifying the construction procedure.
Precast Formwork
Precast formwork plays an important role in modern building, supplying a streamlined technique to creating durable and efficient structures. This technique involves using pre-manufactured mold and mildews, enabling the quick setting up of concrete aspects with precision and consistency. By utilizing precast formwork, building contractors can enhance project timelines and reduce labor prices while guaranteeing top notch surfaces. Comprehending the numerous kinds of formwork available, consisting of standard and cutting-edge remedies, is important for enhancing construction processes and accomplishing desired building results.
6.1 Meaning
Precast formwork describes the technique of building concrete formwork aspects off-site in a controlled atmosphere, permitting accurate measurements and top notch coatings. These precast elements are then delivered to the building site where they are put together to produce the essential framework. This technique enhances efficiency and reduces on-site labor, along with the moment required for traditional formwork techniques.
Precast formwork is particularly advantageous in large-scale jobs where consistency and speed are important. By using precast elements, construction teams can guarantee uniformity in style and efficiency, causing enhanced architectural integrity and lowered dangers associated with weather-related delays. In addition, this method often includes lasting techniques, as excess products can be reduced, and the regulated environment allows using sophisticated healing techniques.
In summary, precast formwork provides a modern-day option to conventional formwork obstacles, producing substantial benefits in terms of high quality, performance, and sustainability in building projects.
6.2 Benefits
Precast formwork is a method extensively made use of in building and construction, entailing the construction of concrete elements in a regulated setting prior to their installation at the construction site. This strategy supplies numerous benefits that contribute to a lot more efficient structure processes and high-grade structures.
One of the primary benefits of precast formwork is enhanced quality assurance. Since the parts are manufactured in a factory setting, the conditions are much more manageable, permitting regular worldly quality and improved dimensional precision.
Speed of building is one more considerable benefit. Precast aspects can be created concurrently while website prep work occurs, decreasing general job timelines. Once the parts prepare, they can be swiftly set up, reducing labor expenses and promoting quick project completion.
Additionally, precast formwork adds to reduced site disturbance. With the majority of the building occurring off-site, the demand for considerable on-site labor and considerable material storage is substantially decreased, leading to a cleaner and more secure construction atmosphere.
Additionally, precast concrete is known for its sturdiness and stamina. The controlled curing environment boosts the efficiency features of the concrete, causing components that can hold up against severe weather conditions and endure hefty tons.
An additional advantage is the adaptability of style. Precast formwork can be built into numerous shapes and sizes, enabling innovative building solutions and personalization to satisfy specific task requirements.
Finally, precast formwork is frequently much more sustainable than typical methods. It creates much less waste, advertises efficient use products, and can incorporate recycled parts, ultimately adding to a reduced ecological effect in construction projects.
6.3 Drawbacks
Precast formwork supplies many benefits in building and construction, however it also includes a number of negative aspects that can affect project implementation and general expense. Understanding these disadvantages is crucial for making notified choices pertaining to formwork types.
- High First Cost: The in advance investment for precast formwork can be significantly greater compared to traditional formwork systems, making it much less easily accessible for smaller tasks.
- Transportation and Taking Care Of Challenges: Precast elements call for mindful transportation and taking care of to stay clear of damages, which can complicate logistics and increase labor expenses.
- Limited Design Flexibility: As soon as precast components are made, making design changes or adjustments can be difficult and expensive, limiting flexibility throughout construction.
- Dependency on Production Set Up: Delays in the manufacturing of precast elements can bring about job hold-ups, impacting the total timeline and coordination.
- Hefty Equipment Requirements: The installment of precast formwork might demand specialized heavy equipment for lifting and placing elements, adding to forecast prices.
- Use Site Room: Keeping precast devices before setup can use up substantial area on-site, possibly impeding various other construction activities.
6.4 Applications
Precast formwork is a crucial component in the building market, providing countless applications that boost the efficiency and high quality of structure projects. This method entails casting concrete components in a controlled setting before moving them to the construction site. The versatility of precast formwork allows its use across a variety of building scenarios, guaranteeing structural integrity while reducing labor and time on-site.
- Residential Buildings: Precast formwork is widely made use of for building walls, floorings, and roofs in household tasks, guaranteeing fast setting up and decreased building time.
- Industrial Construction: In stockrooms and manufacturing facilities, precast elements provide toughness and versatility in design, fitting huge open areas.
- Bridges and Facilities: Precast elements are typically used in the building and construction of bridges and overpasses because of their strength and capacity to withstand heavy lots.
- Parking Frameworks: Precast formwork is optimal for multi-story parking lot, allowing for effective space company and rapid building and construction.
- Preserving Wall surfaces: Making use of precast walls can effectively sustain soil and stop erosion, making them appropriate for landscaping and civil design tasks.
- Sound Barriers: Precast panels are used in creating together with highways and trains to lower noise pollution in adjacent locations.
Shielding Formwork
Shielding formwork is a construction method that combines structure and insulation, creating an extremely effective service for developing walls and structures. This method entails using tough panels that are developed to hold concrete while offering thermal insulation, resulting in energy-efficient frameworks that maintain comfy indoor temperature levels year-round. Shielding formwork not just quickens the building procedure however likewise adds to sustainability by decreasing energy consumption and enhancing the ecological efficiency of buildings.
7.1 Review
Protecting Formwork (IF) represents a modern method to building energy-efficient structures. Combining kind and function, this building method integrates insulation right into the formwork system, simplifying the building procedure while enhancing thermal efficiency. This review explores the main characteristics and benefits of Insulating Formwork in modern building.
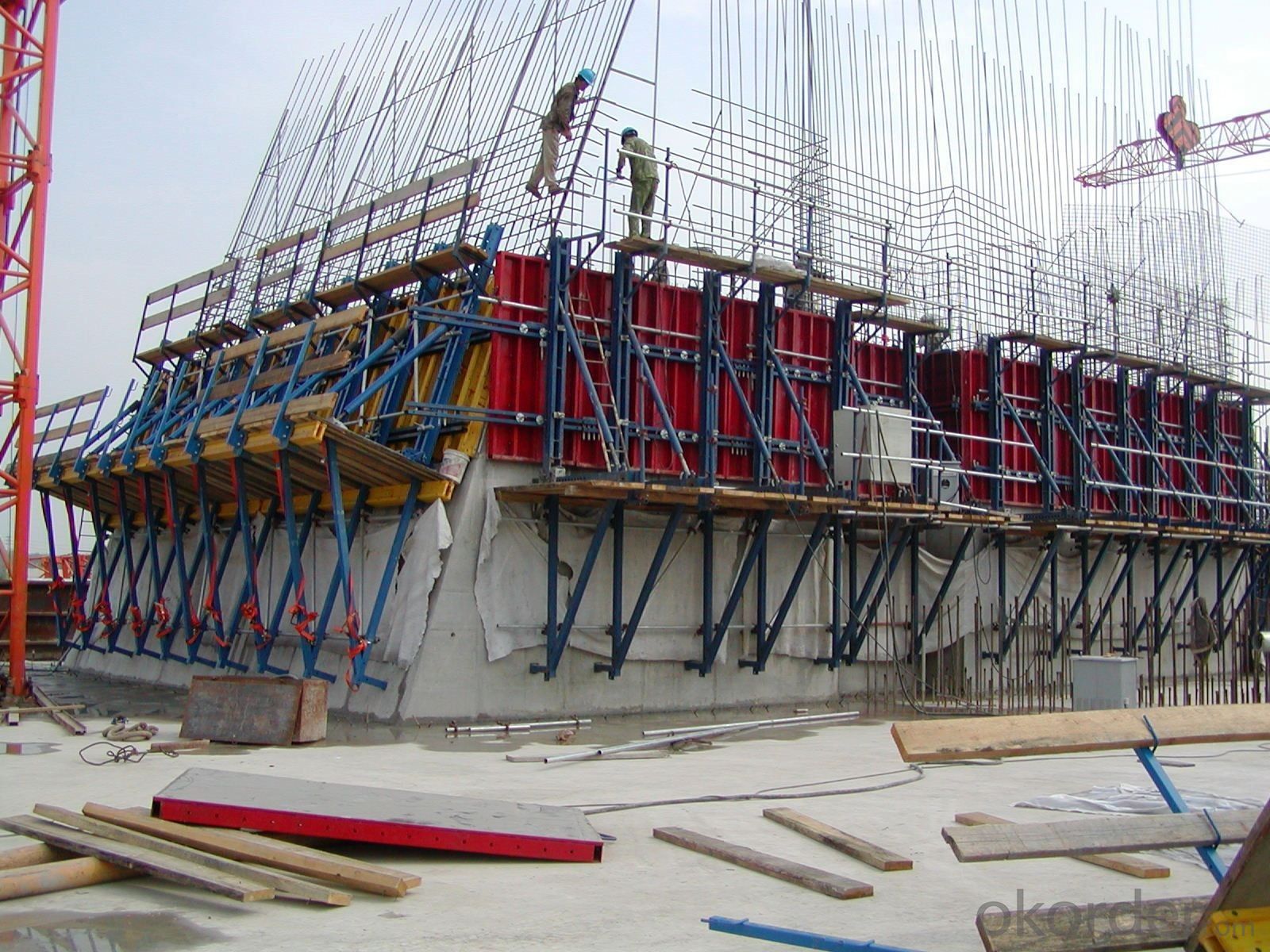
- Power Performance: Shielding Formwork gives remarkable thermal insulation, which can result in significant power cost savings in heating & cooling.
- Structural Stability: The system supports the concrete throughout curing, causing durable and long lasting structures.
- Time Conserving: Quick assembly and reduced labor demands contribute to much shorter construction timelines.
- Cost-Effectiveness: Preliminary investment might be higher, however long-lasting cost savings on energy expenses generally offset these expenses.
- Environmental Benefits: IF can add to sustainable structure methods by enhancing energy efficiency and reducing carbon impacts.
7.2 Advantages
Protecting formwork stands for a cutting-edge method in building and construction that incorporates insulation products with the formwork process. This method not only help fit concrete structures but likewise boosts thermal performance. The following are some remarkable benefits of making use of shielding formwork.
To start with, protecting formwork provides exceptional thermal insulation for structures, lowering power usage and boosting the general energy effectiveness of buildings. This brings about considerable savings on heating & cooling costs with time.
Second of all, the system enables faster building and construction times. By combining insulation and formwork in a single action, labor and material expenses can be reduced, leading to quicker project completion.
Additionally, insulating formwork adds to boosted interior environmental top quality. The thermal mass generated by the concrete helps preserve steady interior temperature levels, advertising comfort and decreasing reliance on mechanical heating and cooling down systems.
Furthermore, making use of insulating formwork can boost the structural integrity of buildings. The continual insulation decreases thermal bridging, which can bring about condensation concerns and potential mold and mildew growth, therefore expanding the life-span of the framework.
Last but not least, shielding formwork promotes sustainability in building and construction. By using materials that boost power effectiveness and lower waste, this technique lines up with contemporary environmentally friendly building methods, aiding to minimize the carbon footprint of new growths.
7.3 Limitations
Protecting formwork, while offering many benefits in building and construction tasks, does have specific restrictions that should be taken into consideration. Firstly, the initial price of protecting formwork products can be greater contrasted to conventional formwork systems. This can be a substantial element for budget-constrained projects.
Another limitation is the complexity of setup strategies that might need customized knowledge and skills. This can cause boosted labor prices and the capacity for mistakes during assembly if workers are not appropriately trained.
Furthermore, the long-lasting resilience of shielding formwork can be a problem. While developed to withstand the pressures of concrete, certain products may break down in time if not properly maintained or if revealed to rough climate condition.
In addition, shielding formwork may not appropriate for all kinds of structures, especially those that call for particular architectural information that are hard to achieve with inflexible types. This limits style flexibility and may require making use of alternate formwork systems for elaborate layouts.
Lastly, there are ecological factors to consider. Although shielding formwork offers power performance advantages, the production of particular insulating materials may have a significant environmental impact. This highlights the relevance of analyzing the whole lifecycle of the materials utilized in the project.
7.4 Regular Applications
Protecting formwork is a building and construction strategy that combines the features of formwork and insulation in building tasks. This method not just supports the concrete throughout curing but likewise supplies thermal insulation, enhancing the energy effectiveness of buildings.
One regular application of shielding formwork remains in the building of shielded concrete types (ICFs) for residential and industrial buildings. These types are made from increased polystyrene or similar products, which remain in place after the concrete has treated, creating a well-insulated wall framework.
Another application is in the construction of structures and walls for energy-efficient structures. By utilizing protecting formwork, building contractors can create durable structure walls that use both structural honesty and exceptional thermal efficiency.
Insulating formwork is additionally useful in the building and construction of preserving wall surfaces, where thermal insulation aids prevent heat loss and includes architectural security. It's progressively used in below-grade applications to boost the power performance of cellars and underground facilities.
In business projects, insulating formwork can be used for building large-scale frameworks, such as storage facilities and shopping centers, providing considerable energy financial savings with boosted insulation residential properties.
Ultimately, this technique is utilized in the building of eco sustainable structures, permitting designers to develop areas that reduce energy consumption and reduce carbon footprints while preserving stamina and durability.